|
Home - Industry Article - Mar 08 Issue |
The Case for Enterprise Cost Systems |
By Matthew Smith, President and CEO, 3C Software
Companies have invested significant resources into ERP systems to integrate a myriad of business functions, including operations, sales, finance and accounting. While their promise of integration is impressive, they consistently fail in delivering one facet vital to understanding profitability for process manufacturers – costing. Using spreadsheet workarounds or developing in-house systems are only band-aids to the larger challenge of calculating and analyzing detailed product cost data in an integrated environment. Enterprise cost systems are designed to handle the rigor required to develop a comprehensive approach to managing production costs.
Since many manufacturers have already implemented ERP systems, questions regarding the need for an additional system to track, analyze and manage costs are no surprise. Does it replace the entire ERP system? What happens to existing ERP cost modules? How do the other ERP modules function properly? Is there additional work for cost personnel? While each Impact: ECS customer uses the system differently, all have found that using Impact: ECS in conjunction with their ERP system has significantly improved their ability to manage costs.
Can ERP Systems Provide Cost Data Most ERP deployments in complex and process manufacturing environments are centered on implementing financial modules to handle transactional accounting and reporting functions. To a lesser extent, these deployments also deliver modules for human resources, procurement and order entry functionality. However, very few ERP deployments in these manufacturing environments have delivered a fully functioning manufacturing module that provides the data needed to develop a comprehensive view of costs. In order to unlock much needed cost information from the ERP system, a separate cost management system operated parallel to the ERP system becomes the most sensible and effective solution. In fact, an investment in Impact: ECS represents an opportunity to leverage large amounts of transactional data into meaningful and actionable cost information. Without Impact: ECS, companies with complex manufacturing processes run the risk of reverting back to spreadsheet solutions that are operated independently and often in conflict with the ERP system.
Effective Cost Management The laws of economics state that the market, not the manufacturer, determines the price for commodity products. With advances in productivity and increased global competition, market prices for commodities continue to fall. Simultaneously, issues like underutilized capacity and depressed demand for goods results in higher costs for manufacturers. These conflicting forces create slim and sometimes negative profit margins for commodities producers, forcing them to focus on better cost management as the main component of their survival strategy. Effective cost management begins with understanding costs. A company that knows its costs and understands the details behind acquiring raw materials, operating equipment, routing production, producing goods and shipping products to end users has the best chance of increasing its profit margins in today’s competitive environment. To reach that level of cost understanding, detailed data collection, custom calculation execution, scenario analysis and frequent reporting are all required.
The Challenge of Understanding Costs So what is it about complex and process manufacturers that make understanding costs so difficult? The answer – the process itself. Cost managers have to account for complexities like raw material yields or machine variances that do not exist in assembly-line production models. Most ERP systems contain some level of cost management functionality. In fact, all ERP systems have the capability to roll up finished goods costs, manage bills-of-material, report actual spending, calculate the cost of goods sold and value inventory. These capabilities certainly meet regulatory reporting requirements and produce a high-level view of costs, but they fall short in delivering information that leads to a true understanding of costs within a production environment. The following scenarios describe some of the difficulties that cost managers face when working to uncover costs.
Bill of
Materials
- The BOM does not capture the entire set of costs generated from producing goods.
- The same product is produced on many different machines or product lines resulting in multiple costs for the same finished good.
- BOMs may change depending on the process line or machine used to make the product.
Inventory
- Product converts to another product at some point in the process.
- Base products are produced and staged as work-in process (WIP) and then used to produce many different finished products.
Specialized Processes
- Production process includes disassembly steps in addition to traditional assembly-only processes creating yield loss and gains that require cost and BOM adjustments.
- Customized cost computations based on market values are required in instances where co-products and by-products, or credits may be issued to accurately reflect the cost of the finished goods.
- Off-quality and downgraded products when produced will need special cost computations or unique packaging of items that results in an explosion in the number of finished goods.
The list of challenges is endless and traditional ERP solutions do not have the flexibility to adjust to these complexities when calculating costs. And, because each company has its own unique costing methods, it becomes virtually impossible for any rigid cost module to effectively adapt to any environment.
Impact: ECS Plus ERP The need for supplemental cost management systems has not gone unnoticed by ERP system users or vendors. A number of efforts are underway at manufacturers around the world to customize current ERP systems, develop new modules and even establish partnerships between vendors and users to improve existing methods. However, in almost every case, cost managers have resorted to using unsecured, stand-alone spreadsheets to get the needed information about costs.
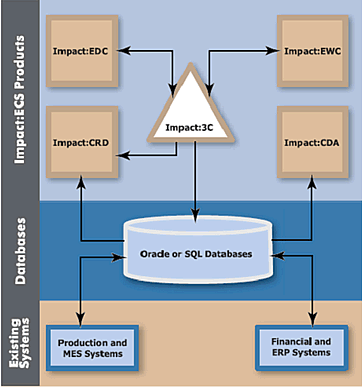
Unfortunately, many legacy systems that should have retired after installing the ERP system are still used and supported to develop cost data, resulting in frustrated end-users and IT staff. Certainly, Impact: ECS does not replace the existing ERP system, nor does it have to replace the ERP system’s cost module. The solution developed by 3C Software enhances the value of existing ERP systems by delivering a cost management system that incorporates ERP data to improve the accuracy and relevance of cost data. Without duplicating the efforts of cost personnel, Impact: ECS provides an environment where unique cost calculations are performed and resultant cost data is published back to the ERP system for use in the company’s financial reporting and analysis. The following are examples of how Impact: ECS can compliment the company’s current ERP strategy:
If the ERP system houses the primary BOM then Impact: ECS can access that information directly to calculate production costs. In instances where alternate BOMs are needed to reflect the actual manufacturing environment, Impact: ECS can store the additional BOMs and generate cost information based on the alternative’s requirements.
Primary process flows or routings, for finished goods that are stored within ERP systems are easily accessed. Impact: ECS can capture this information as well as store alternate routings and compute corresponding costs for each.
In instances where the standard costs are blended averages of many different costs, Impact: ECS can compute each unique cost, calculate the blended average, and upload the resultant costs into the ERP cost module.
If the shop-floor, manufacturing execution system or process data historians provide actual production data, Impact: ECS can calculate actual costs and compare them to the standard costs from the ERP system.
Impact: ECS’ flexibility allows it to conform to the unique needs of complex or process manufacturers. Based on the level of ERP implementation, type of cost information needed and the availability of data, Impact: ECS cost models are designed, built and integrated to meet the needs of each company individually. In cases where few or none of the ERP system’s manufacturing modules are implemented, the cost management system by 3C Software can serve as the bill-of-material, process routing and product master system. Since the source code is not changed in developing these unique cost models and the end-user has access to the tools used to build and maintain the models, Impact: ECS is easily modified and updated to keep pace with the current needs of the company. The result of implementing Impact: ECS is a highly customized cost management system that meets the unique needs of the company, integrates into existing ERP systems and provides security for sensitive information – all resulting in increased understanding and awareness of production costs within the organization.
Matthew Smith is President and Chief Executive Officer of 3C Software, the supplier of ‘best-of-breed’ cost management solutions to companies with complex or process-intensive manufacturing. He sets the strategic direction of the organization. Prior to taking the leadership post at 3C Software, Matthew has served many vital roles. Joining 3C Software in 1993 as a sales consultant, he gained experience in effective cost accounting practices across the many industries 3C Software serves. Matthew continued to progress through the organization as Director of Business Development and Sales where he was responsible for forming relationships with new and existing cost management clients. From there, he moved on to the role of Executive Vice President where he oversaw all operational areas, including marketing, consulting, support, and strategic planning. Matthew is consistently recognized for his expertise in developing and implementing enterprise cost systems and has been an invited speaker at many industry-specific conferences and trade shows. He infuses 3C Software with his own brand of passion and leadership and provides insight to his employees in the area of enterprise cost management. For article feedback, contact Matthew at
matthewsmith@3csoftware.com
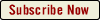
|
|
|
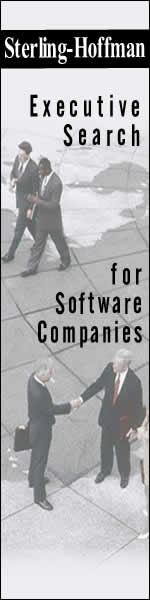
|